Аўтаматычная лінія па вытворчасці 2/3/5/7-слойнага гафрыраванага кардону
Description
Fully automatic corrugated cardboard production line is used to produce corrugated cardboard with different layers, including 2-layer, 3-layer, 5-layer and 7-layer structures. It usually includes automatic paper feeding, corrugated roll pressing, glue bonding, cardboard forming, drying, cutting and stacking, etc. It is capable of fully automated production from raw materials to finished products.
Тэхнічны ліст
мадэль | WJ200-2200-5PLY |
Grade | Min. B |
Moisture content | 11% ± 2% |
Face paper | 100~250 g/m2 |
Liner paper | 100~250 g/m2 |
Corrugated paper | 100- 200 g/m2 |
Flute profiles | A,B,C,E,F,G flute |
Steam requirements | 8-10 Kg |
Steam consumption | 2500 kg/h |
Air compressor pressure | 0.8~1.1 Mpa |
Electricity | 380V, 50Hz, three-phase four wire type |
* Equipment Direction | Left or Right transmission will be as required |
* Factory request size | Specific length as to the foundation of drawing |
* Note: the roll paper which is used to test the corrugated cardboard production line speed should meet above requirements.
Асноўныя рысы
1. High degree of automation
The corrugated cardboard production line can realize the fully automated production process from raw materials to finished products.
2. High production efficiency
Through automation control, it improves production efficiency and reduces labor cost, and at the same time, it can realize non-stop order change and improve production continuity.
3. Energy saving and environmental protection
The requirements of energy saving and environmental protection are taken into account in the design, and energy consumption and material waste are reduced by optimizing the production process and equipment configuration.
4. Intelligent management
Combined with Industry 4.0 technology, it realizes intelligent management of the whole corrugated cardboard production line and intelligent control from customer order to production to logistics packing.
5. Stability and reliability
Adopting advanced technology and equipment to ensure the stability and reliability of the corrugated cardboard production line and reduce the failure rate.
6. Precise control
Through advanced control technology, it realizes automatic monitoring and adjustment of raw paper feeding temperature, humidity and tension, so as to precisely control the physical properties of raw paper.
7. Green design
Resource consumption, ecological and environmental impacts as well as human health and safety are taken into account in the design, which meets the requirements of green design.
8. Safety performance
The corrugated cardboard production line is designed with full consideration of mechanical and electrical safety to ensure the safety of operators.
9. Strong adaptability
It can adapt to the production demand of multi-specification and multi-species to meet the diversified order requirements of the market.
10. Production management system
Equipped with production management system, it can realize the collection, statistics and printout of production data and improve the production management level.
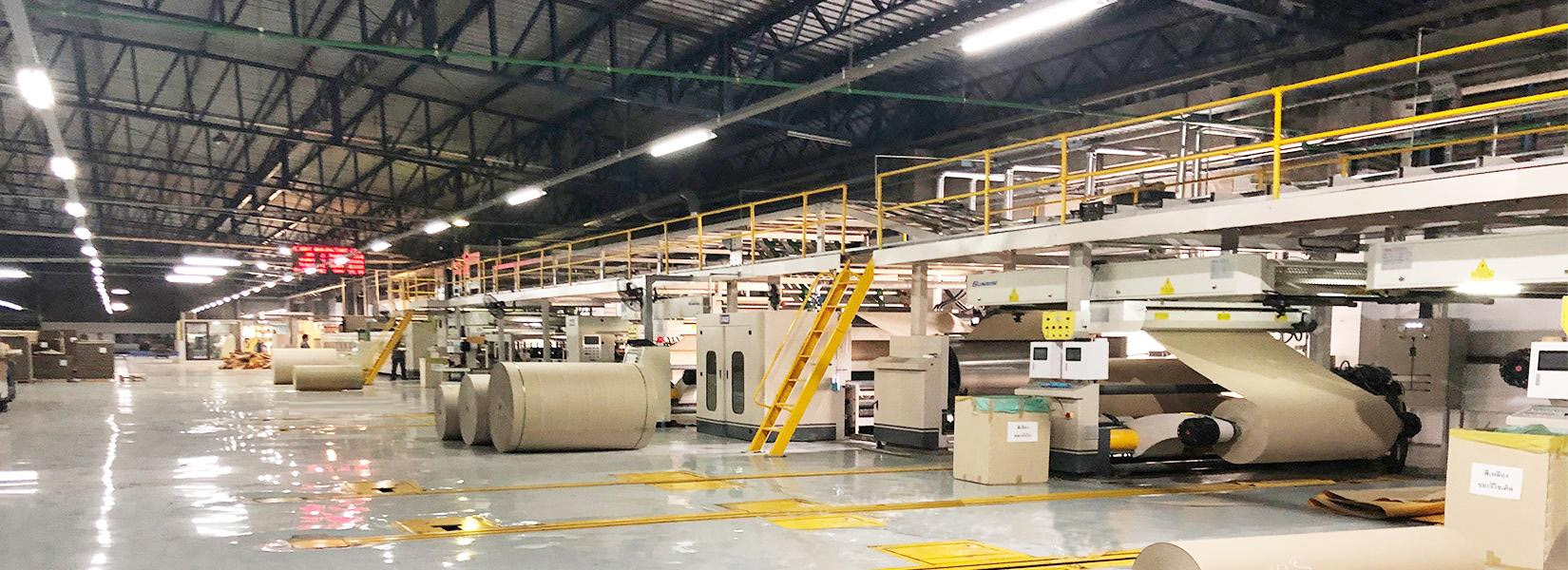
Спіс канфігурацыі (пачатковая частка)
No. | Імя | Qty | Feature |
1 | RSH Hydraulic Mill Roll Stand
( with trolley and track) |
5 | –Main shaft φ242mm,double curve heavy rocker arm, tooth chuck, pneumatic type multi point brake,hydraulic lifting,left and right translation
–Guide rail length is 6000 mm, the trolley adopt 10 mm plate welding |
2 | Auto-Splicer | 5 | –Keeping the corrugated board line uninterrupted working, reducing paper loss and greatly improving productivity |
3 | PH-90 Pre-heater | 4 | –The roller φ900 mm, Electric adjustment angle, adjusting heating area within the range of 360 ° |
4 | SF-A22Single Facer | 2 | –Corrugated rollerφ360mm, 48CrMo high quality alloy steel,plating tungsten carbide
–Independent gearbox,universal joint drive structure –Cylinder control lifting –Pneumatic control glue,circulating supply glue –Man-machine display |
5 | OBH Conveying Bridge | 1 | –The main beam is connected with the GB 200 channel steel, 200H steel, 63 angle steel
–Independent frequency motor drive paper conveying –Suction tension and electric correcting |
6 | Trriplex Pre-heater | 1 | –The rollerφ900 mm,electric adjustment angle angle , adjusting heating area within the range of 360 ° |
7 | GM-20 Glue Machine | 1 | –Glue roller φ269mm , carved 25 line pit type mesh –With preheater device
–Independent frequency motor drive –Circulating supply glue with PLC control –Man-machine interface display |
8-14 | DF-60 Double Facer, etc. | 7 | Калі ласка, звяжыцеся з намі для атрымання больш падрабязнай інфармацыі |
Chuang Xin Carton Machinery з'яўляецца вядучым вытворцам і пастаўшчыком рашэнняў для ўпаковачных і друкарскіх машын. Кампанія CX Machinery, размешчаная ў горадзе Чанша, сусветна вядомай сталіцы вытворчасці ўпаковачных матэрыялаў, была створана як частка Carton Machinery and Printing Equipment і зарэгістравана CQC у адпаведнасці са стандартамі ISO14001 і OHSAS 18001. У нас ёсць каманда інжынераў з больш чым 10-гадовым вопытам вытворчасці ў галіне кардоннага абсталявання, а таксама наша ўмелая каманда продажаў, каб забяспечыць поўную падтрымку нашых кліентаў.
CX Carton Machinery распрацоўвае, вырабляе і прадае высакаякаснае ўпаковачнае абсталяванне для кардоннай каробкі, такое як завод па вытворчасці гафрыраванай каробкі, лінія па вытворчасці 2/3/5/7-слаёвага гафрыраванага кардона, высечка для флексографскага друкаркі, ротарная высечка, ротарная высечка для кардонных кардонаў. У дадатак да вытворчасці вышэйзгаданых машын, CX Machinery імкнецца да гнуткай налады некаторых дапаможных машын для вырабу кардоннай каробкі.
З нязменнай якасцю і выдатным сэрвісам з 2009 года мы ўстанавілі глыбокія дзелавыя партнёрскія адносіны з замежнымі кліентамі ў больш чым 40 краінах.
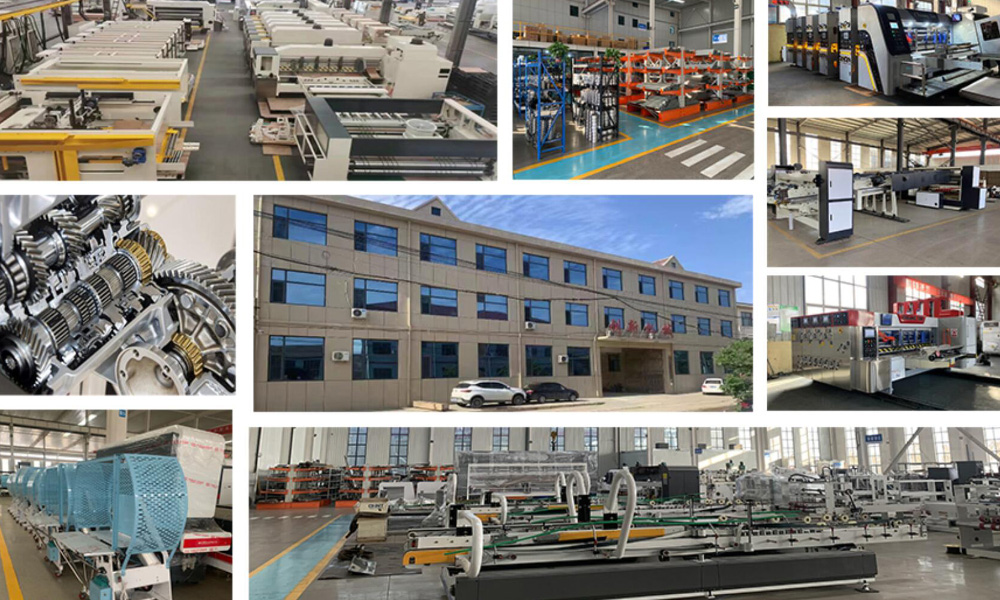
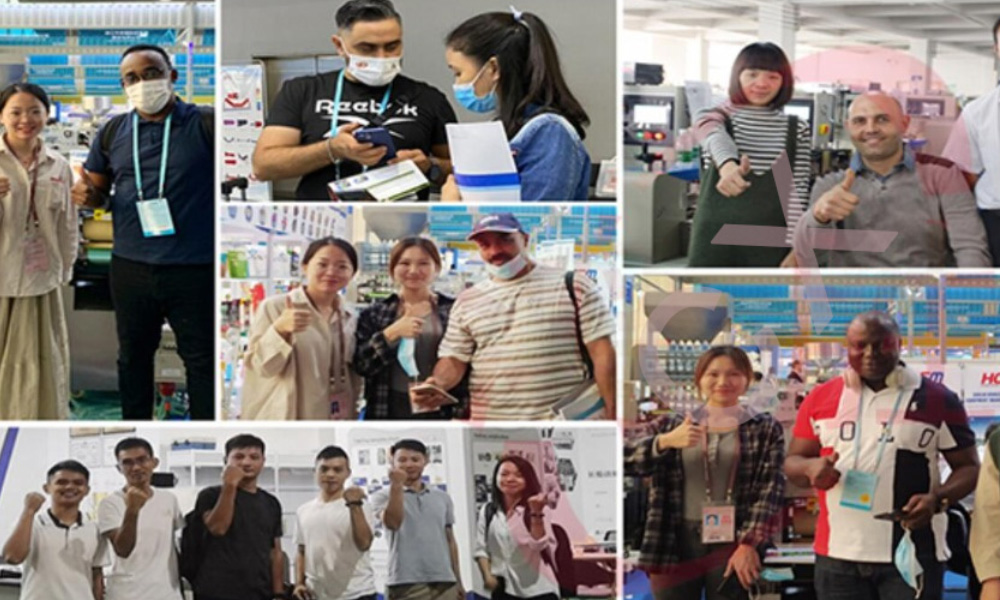