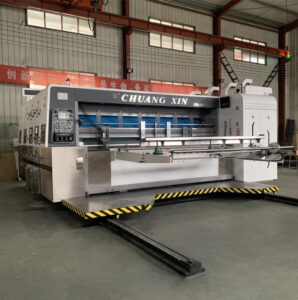
Willkommen in unserem Blog, der der faszinierenden Welt der Schlitzmaschinen für den Kartondruck gewidmet ist. Hier vertiefen wir uns in die komplizierte Funktionsweise und den immensen Wert, den diese Maschinen für die Verpackungsindustrie bringen.
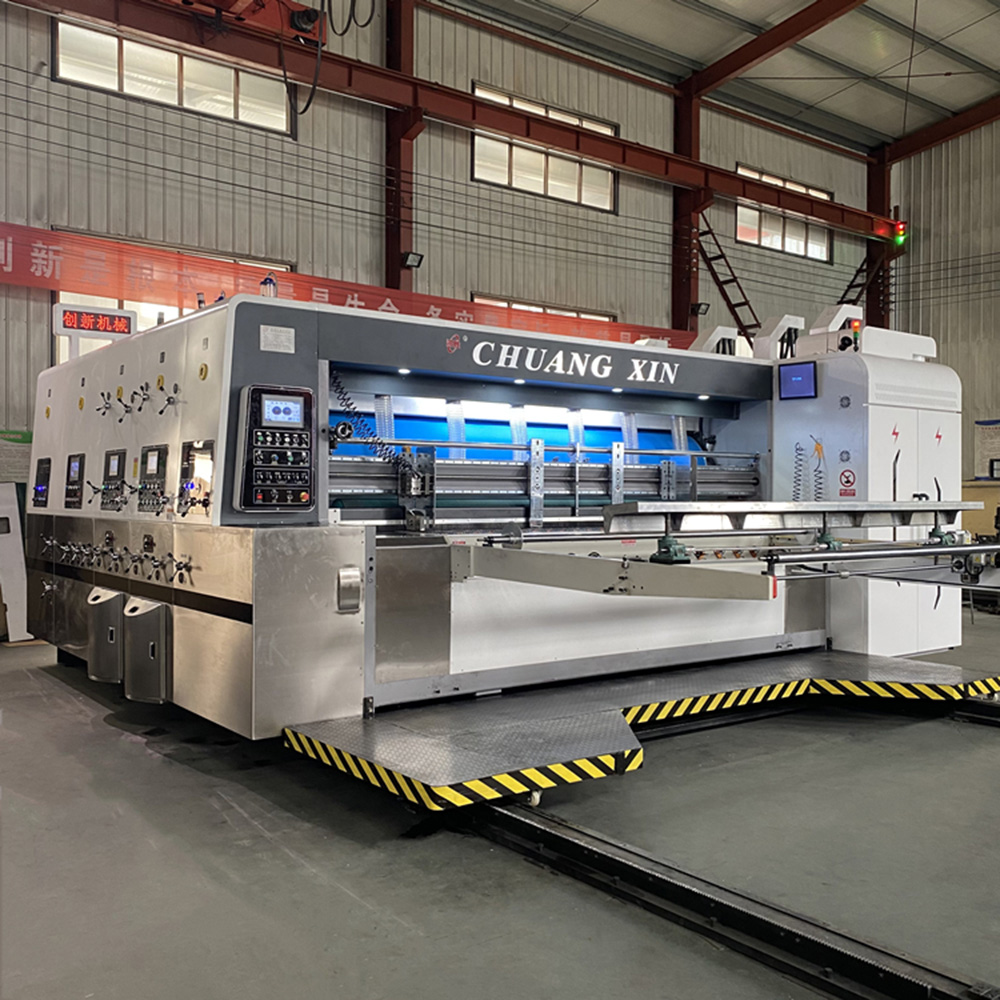
5 Tips for Optimizing Your Corrugated Flexo Printing Machine
Flexographic printing on corrugated packaging is an art as much as a science.
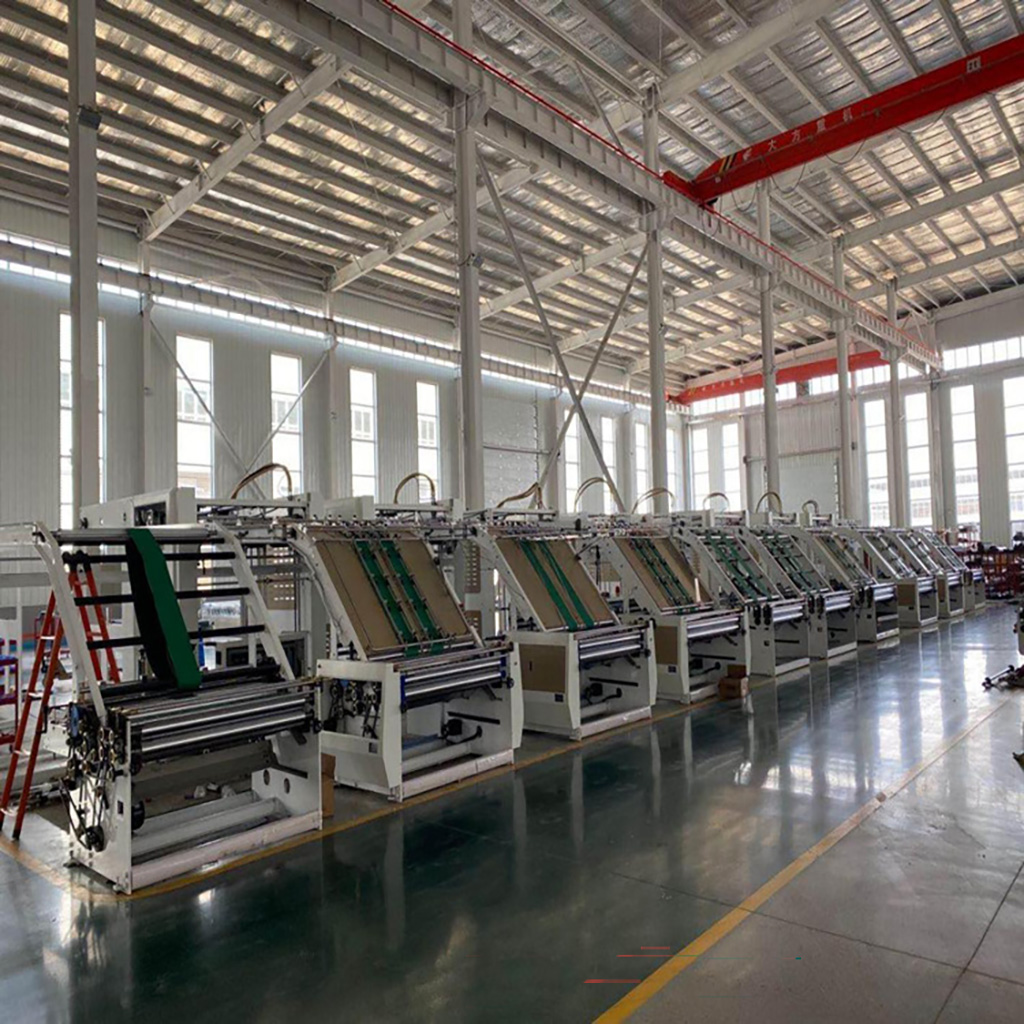
So wählen Sie eine Wellenlaminiermaschine aus
In der heutigen schnelllebigen Geschäftswelt ist Effizienz das A und O. Wenn es um die Aufbewahrung und Präsentation von Dokumenten geht, kann eine Hochgeschwindigkeits-Laminiermaschine für Papierrillen von unschätzbarem Wert sein.
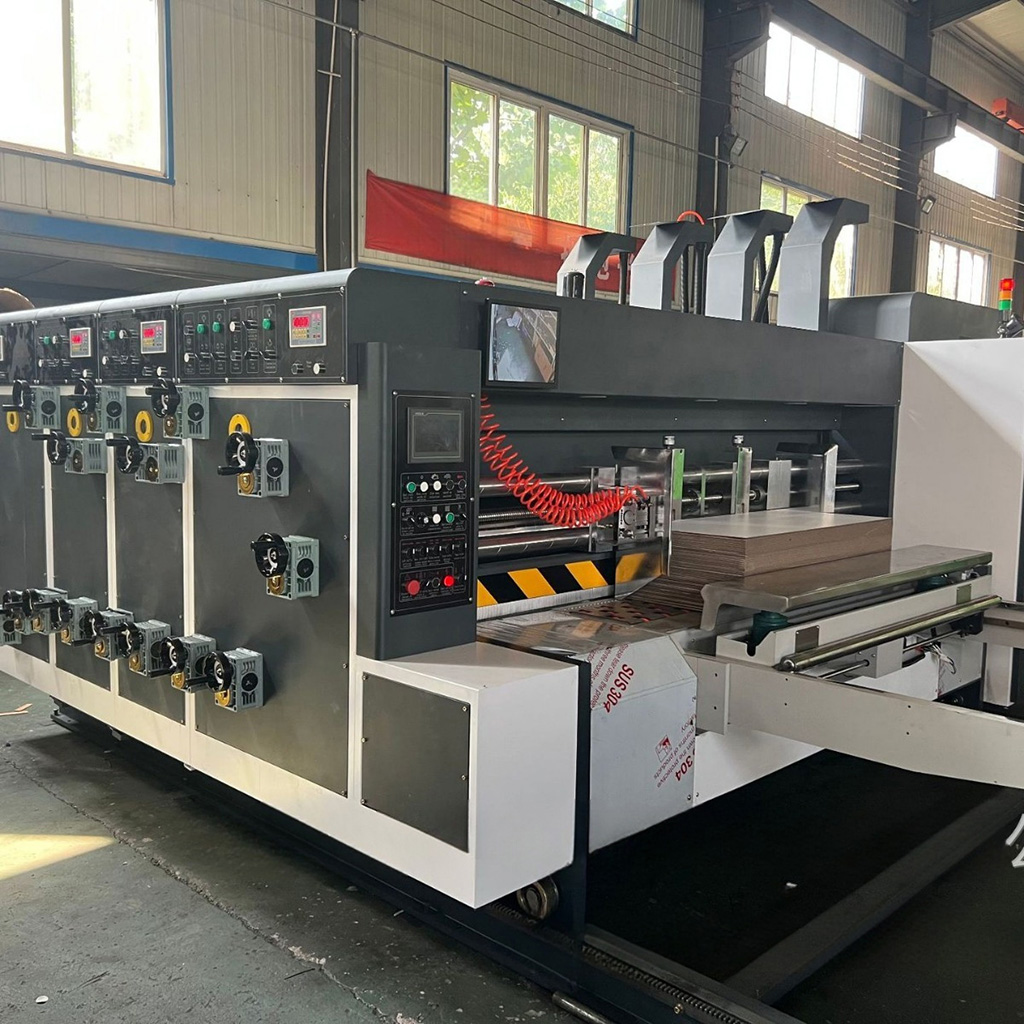
Wie funktioniert ein Druckschlitzer?
Der Druckschlitzer, auch Schlitzmaschine oder Nutfräse genannt, ist ein leistungsstarkes und vielseitiges Metallbearbeitungswerkzeug, das überwiegend zum Bearbeiten von Passfedernuten, Schlitzen und Innenprofilen in Werkstücken verwendet wird.