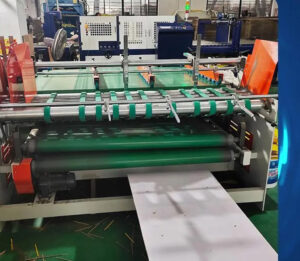
Welkom op onze blog gewijd aan de fascinerende wereld van de kartondrukmachines. Hier verdiepen we ons in de ingewikkelde werking en de enorme waarde die deze machines voor de verpakkingsindustrie bieden.
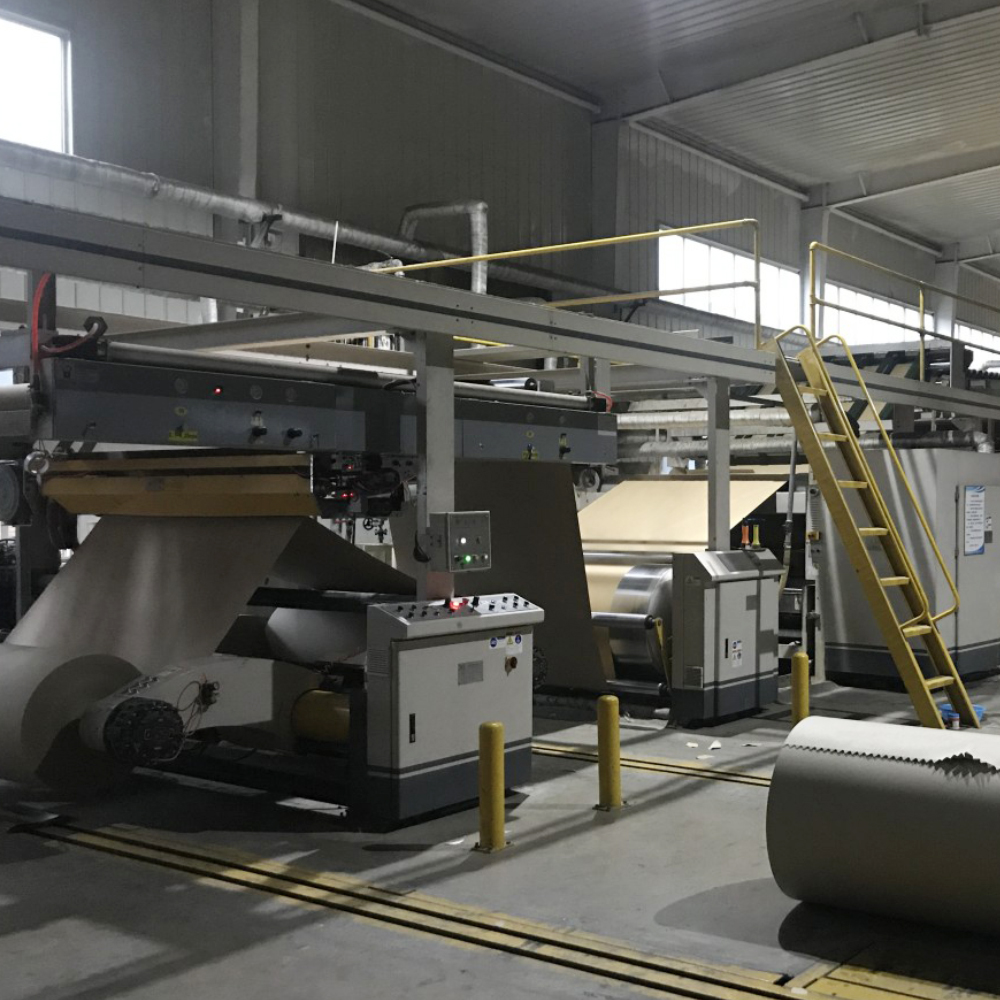
Essentiële componenten van de productielijn voor golfkarton
In de verpakkingswereld zijn productielijnen voor golfkarton onmisbaar.
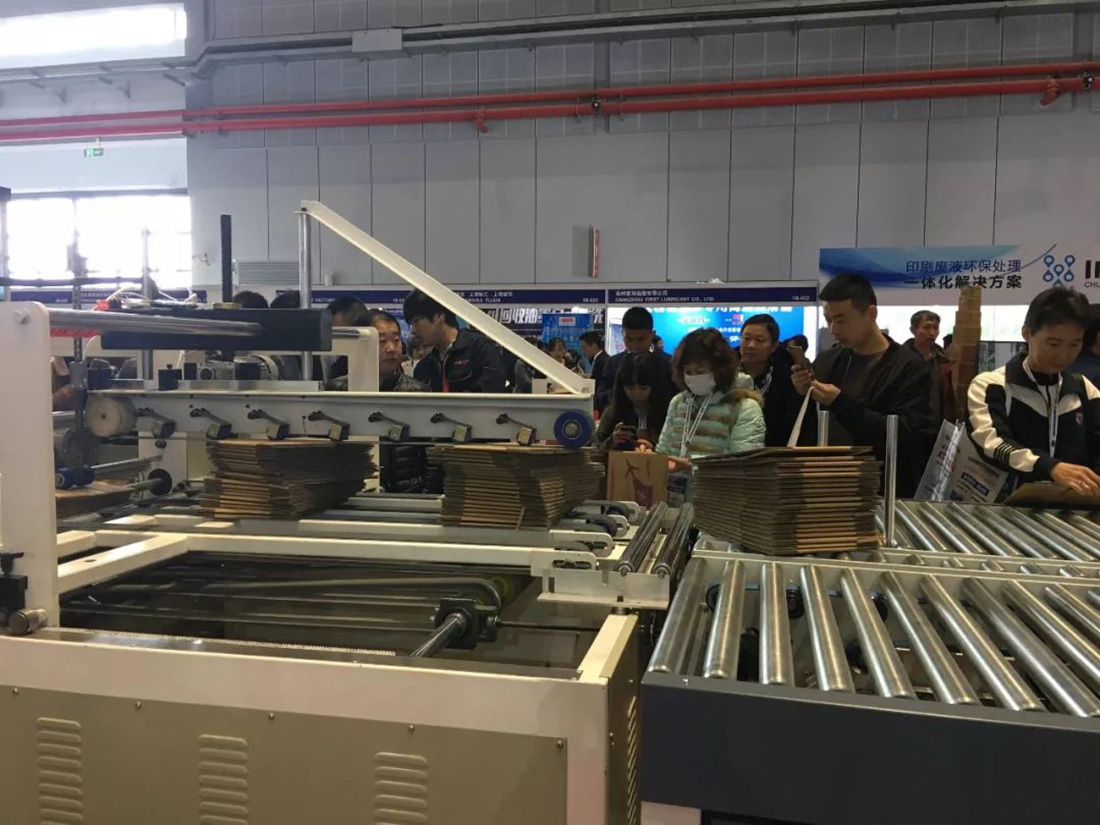
Kwaliteitscontrole in de productielijn van golfkarton
De productie van golfkarton omvat een zorgvuldig georkestreerde reeks fasen, die allemaal een integraal onderdeel vormen van het vervaardigen van duurzame en veelzijdige verpakkingsmaterialen.
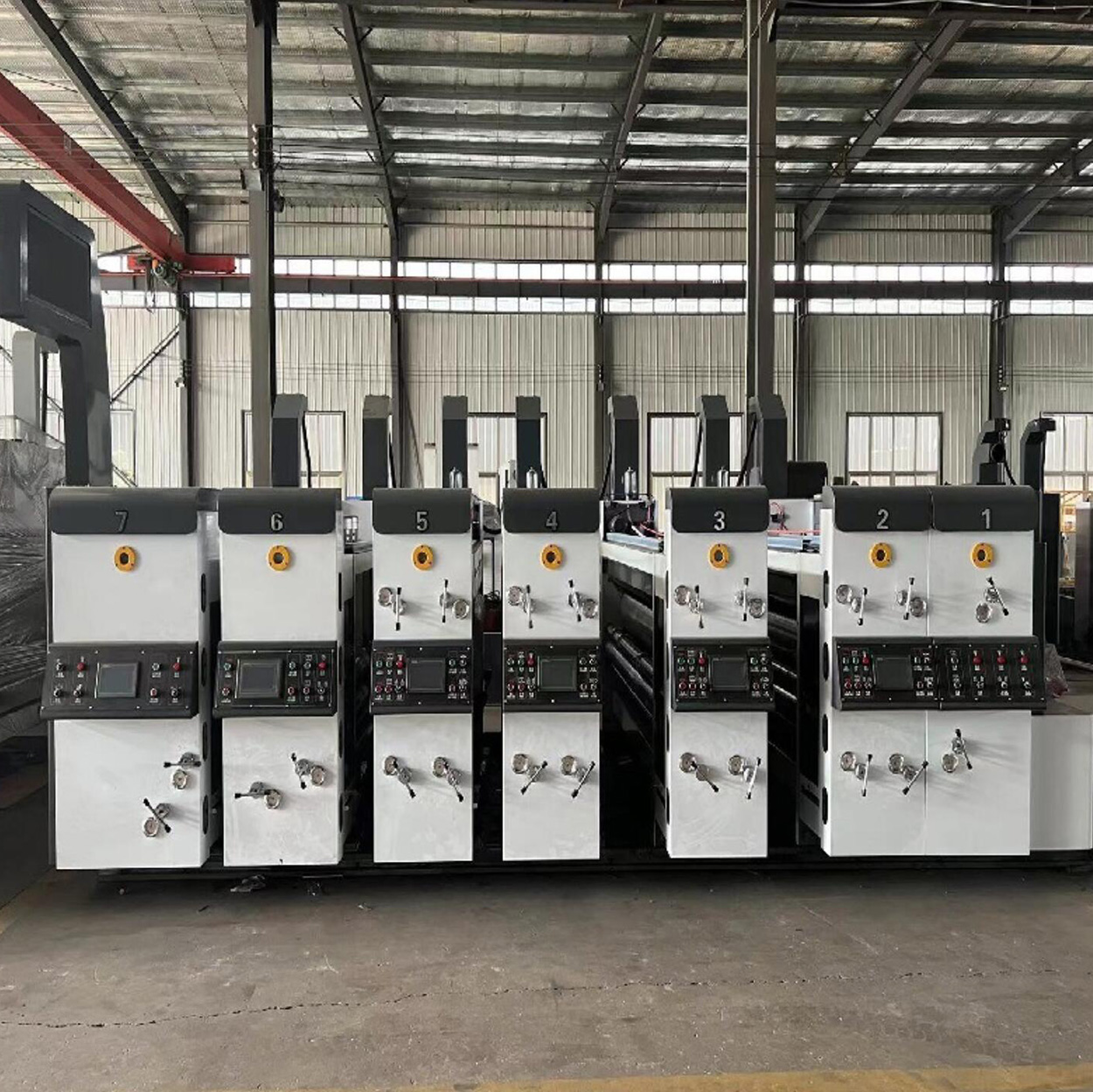
Begrijp het werkprincipe van een kartondrukmachine
Kartondrukmachines zijn essentieel in de verpakkingsindustrie en zorgen voor een efficiënte en nauwkeurige bedrukking van verschillende soorten dozen.