
Karton baskı slot makinelerinin büyüleyici dünyasına adanmış blogumuza hoş geldiniz. Burada, bu makinelerin ambalaj endüstrisine getirdiği karmaşık çalışmalara ve muazzam değere değineceğiz.
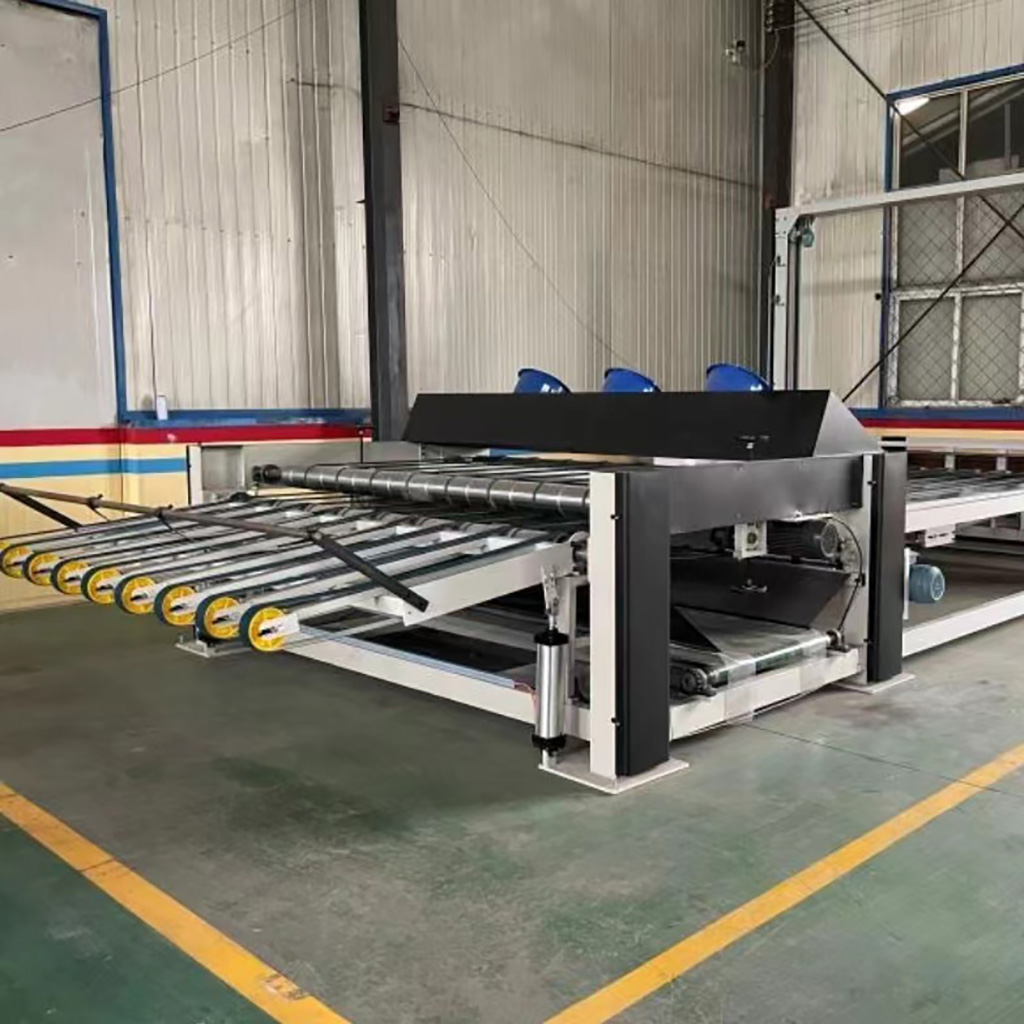
Verimliliği ve Güvenliği Optimize Etmek için İstifleme Makinesi
İstifleme makineleri, modern üretim ve paketleme endüstrilerinde ürünlerin organize edilme, taşınma ve depolanma biçiminde devrim yaratan bir gerekliliktir.
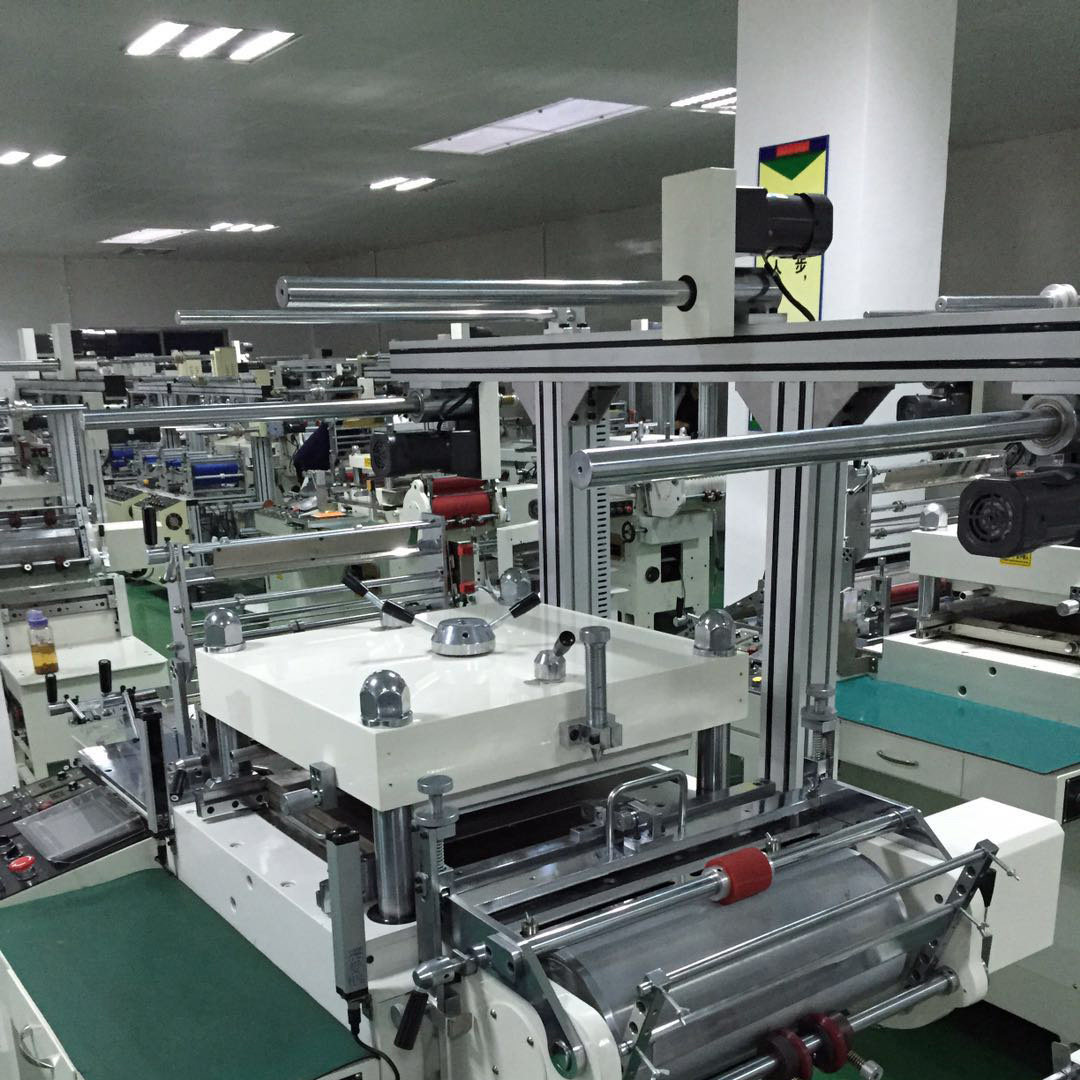
Kalıp Kesim İşlemindeki Adımlar Nelerdir?
Çeşitli malzemelerden şekilleri kesmek için keskin bir kalıp kullanma işlemi olan kalıpla kesme, işçilik ve scrapbooking'den paketleme ve imalata kadar çok sayıda endüstride kullanılan çok yönlü bir tekniktir.
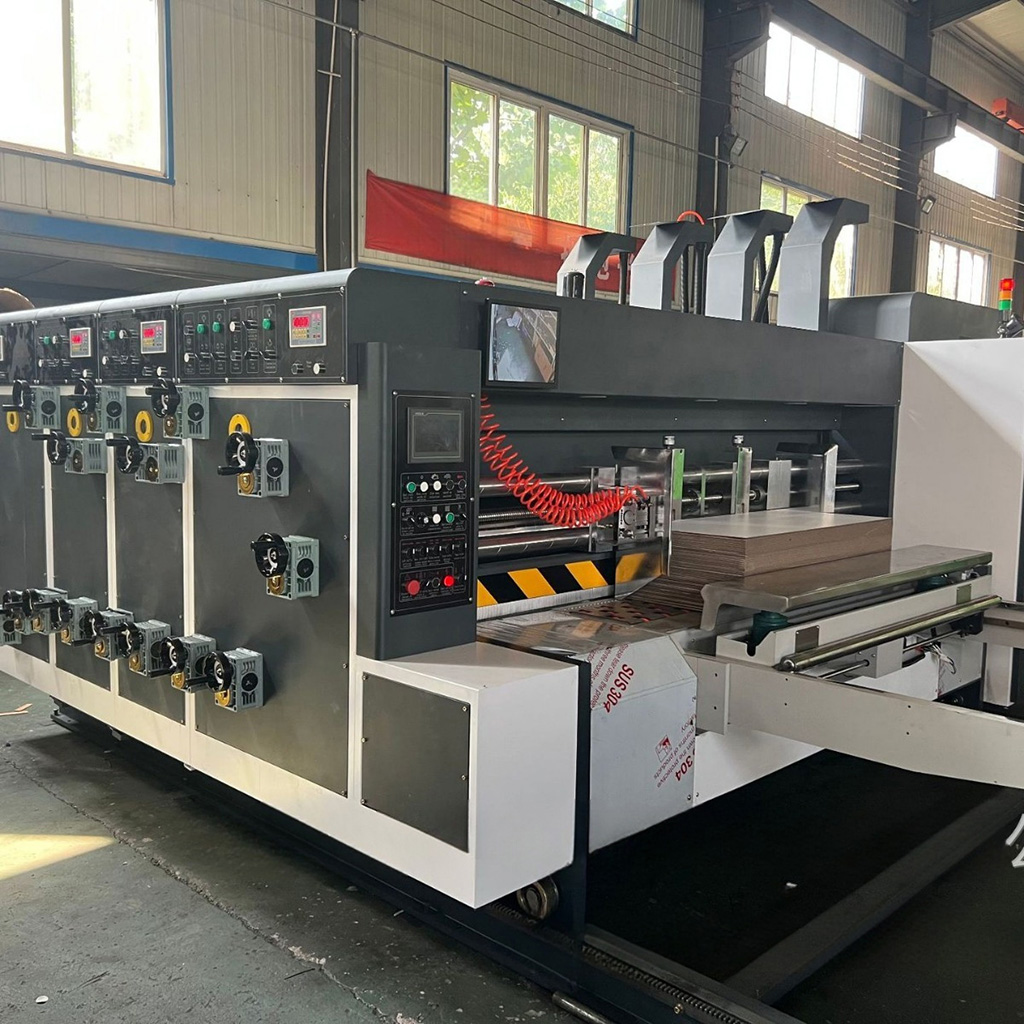
Baskı Slotter Nasıl Çalışır?
Kanal açma makinesi veya kama yuvası kesici olarak da bilinen baskı oluk açma makinesi, ağırlıklı olarak iş parçalarındaki kama yuvalarını, yuvaları ve iç profilleri işlemek için kullanılan güçlü ve çok yönlü bir metal işleme aletidir.